How to Make Wood Pellets with Sawdust
Wood pellet as a kind of new green energy has been widely applied in Europe, South American and other countries around the world. As people become more and more concerned about the carbon emission and air pollution, wood pellet are popular for room heating and for commercial use in power station. If you have a pellet stove or pellet fireplace in your family, then pellet fuel is an easy and clean fuel for family use. Of course, you can buy the pellets from the wholesale market or from the truck transmit system. But, if you have live a place which have plenty of raw material for pellet mill, like sawdust, agriculture waster or other waste thing like fruit shell, grass, garbage etc. Then why not try to make pellet from those waster things before? It is cost saving and easy for use. If you can make those waste things into precious energy, then you saved a lot of money. Now, do you have decided to make wood pellet pellets by yourself?
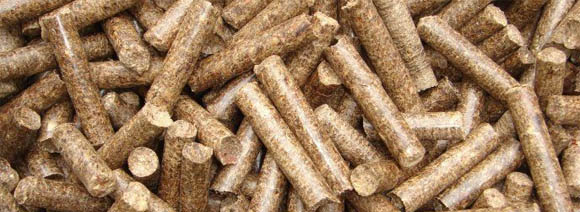
You can save money on heating by burning wood pellets in a wood pellet stove or pellet insert. Pellet stoves are a modern version of the old-fashioned wood-burning stove. However, these stoves are more energy efficient and easier to install and run than the wood-burning models. Wood pellets are made from compressed biomass materials such as crop waste, cardboard, recycled paper, leaves, lawn clippings or sawdust using the wood pellet mill. By using these renewable resources as raw material, pellets are an excellent "green" solution for home heating. The sawdust also can be pressed in to wood pellets, then we will give you some steps to tell you the process on how to make wood pellets with sawdust.
Pellet mill selection
At first, you have to purchase a set of pellet mill which can meet your demand. Of course, there are plenty of types of pellet mill on the market for sale. There are verified in quality and production capacity. In general, the home use pellet mill can meet your demand if you are the first time to make pellets. Also the pellets are only for room heating use. A small pellet mill can be your perfect selection.
Then what is a small pellet mill? A small pellet mill is actually means the flat die pellet mill which are common on the market. It has simple structure which mainly contains a flat die and a compression roller. The basic working principle of flat die pellet mill is that the materials being compressed between the roller and die, then pass through the hole of the die, the cylinder shape pellets are formed under the strong friction force. While the flat die pellet mill can only be used for small production ability. For large scale commercial production, ring die pellet mill is more perfect. Due to the high production efficiency and production cost, ring die pellet mill can not used for home use. While if you have plenty of money, you can chose small ring die pellet mill also. But here, we take flat die pellet mill as an example.
Materials collection and preparation:
After we have purchase a proper pellet mill, the next thing we have to notice is the technology process.
Another thing you have to concern about is to collect the materials. Maybe, you need a car to transmit the material like sawdust, wood branch or other biomass plants to your home or backyard. Actually, the transmission fee is a big problem for cost saving. Long distance transmission is not advisable for use. Of course, the material must be fit for production. Sometimes we need to process them at first according to the production requirements. A hammer mill may be used to make the materials have the same particle size. The length should be less than 6mm. The particle size effect the efficiency of pellet making. Uniform in size can clocked the machine sometimes.
Also the other factor that decided the pelletizing process is the moisture content of the materials. The perfect moisture content is between 12-14%. At this situation, the pellets have the best pellet quality and good shape. If the material is too dry, the pellets are loose in shape which is easy to break for hand touch. In addition, the too wet materials can not make pellets or make the machine slip. All you have to do is to dry the raw material under sunshine for a few days. If necessary, a dryer can be used to dry the materials. As for the too dry of the materials, spay a little water on the materials maybe a good way.
Before feeding the sawdust into the pellet mill, the operator should test the moisture content of sawdust first. The optimum moisture content of the sawdust is 10-15%. The sawdust with higher moisture content should be dried before entering the pellet mill, while the lower one can skip the procedure. For the storage of sawdust, the sawdust with high moisture content should be stored separately from sawdust with low moisture content. Generally, bulk sawdust of 7 m³ with the moisture content around 50-55% are needed to produce 1 ton pellets with the pellet mill.
Screening: The screening of sawdust is an important step before making wood pellets with the pellet mill. The purpose for screening of the sawdust is to remove the impurities, such as stones, plastics, metals and other hard materials in the sawdust that may influence the working efficiency or even lead to serious wearing of the pellet mill. The stones and other hard materials in the sawdust can be removed by a stone trap. While the metal debris can be picked out by a magnet.
Mixing: sometimes a bounder is needed to make pellets. For material which is difficult for making pellets, a addictive of bounder can be added for good quality of pellets.
The process:
Now, you have good preparation for making pellets. The pellet mill is proper, the materials has the proper particle size and moisture content. All you have to do is the careful process technology.
Steps of Sawdust Pellets Making Process:
1. Start the biomass pellet machine in which you will make your pellets and wait a few minutes for heating up the ring die. The heat could help the lignin in the wood fiber out of the sawdust, and bonding the sawdust as the pellets.
2. Put a large box under the chute of the biomass pellet machine for catching the pellets during pelletizing process. Feed the sawdust by handfuls or small shovelfuls into the hopper of the pellet mill. In a few seconds, pellets will begin to fall out of the chute into the box.
3. Allow the pellets to cool in the box before you handle them. When they are cool they are ready for you to burn in a pellet stove or a pellet insert. Store any unused pellets in bags in a dry place.
4. Sieve the pellets that did not form properly. Some pieces will fall apart or break during the pressing process. Separate the improperly formed pieces by shaking or sifting them through a screen.
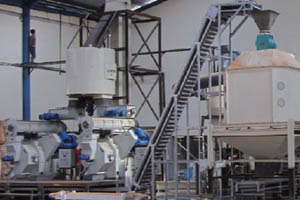
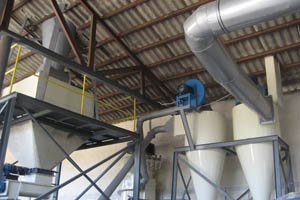
Checking:
The pellets should come out of the biomass pellet machine hard and shiny. If they are mushy there is too much moisture in the sawdust. Allow it to dry out and try again. If the pellets are crumbly there is not enough moisture in the sawdust. Add water with a spray bottle to a small amount of sawdust and mix well before feeding it into the mill. It should take only one or two tries for you to get a sense of the correct amount of moisture required. You can ask local lumber yards for sawdust but make sure the sawdust is clean and is not from chemically treated wood.
Maintaining:
It seems that after you have pelletized the wood pellet you have done all the things you have to do. But there also have some important point you must to know, and have to follow to do.
Firstly, you should clean the die and rollers carefully. When you feed the machine with raw materials, there may have some hard impurities got stuck and if you don’t clean them out, it will be very harmful to the working station of the machine. Furthermore, you may not forget the bearings. The bearings will be working in a high temperature and high press, so maintain the bearings is very important.
Here have some advices and you can take based on your own situation. Before the mill begins to work, you can grand the die with the mixture of bran and oil. And the clearance between the template and pinch roller should be 0.1-0.3mm. Then, you should clean the bearing every 2-5 days and fill it up with grease that resist to high temperature. You also have to know that all the maintenances thing must be done in the state of blackout. And the machine should be placed suitable and stable, because it is not good to the mill if you move it constantly.
If the pellet mill has low production, there are several reasons should be concerned:
1. New die. Please check up whether the compression ratio is matching up to the raw materials at first. If the compression ratio is too big, the resistance force that material pass through the die holes are increasing, the extruding pellet is hard and the output is lower; if the compression ration is so small that the extruding pellet can not molded. So it is necessary to choose a proper compression ration one more time. The second is to check up the degree of finish of holes of ring die. Bad quality ring dies has rough surface of ring die holes, and the resistance force of discharging is so big that the surface of the pellets is rough with low output. At last, check up the round ring die is out-of-round or not. This can give rise to lower output of the pellets. So it is necessary to choose a high quality ring die.
2. After the flat die is in operation for a period of time, please check up whether the taped holes of inside flat die is wearing or not, and the compression rollers are wearing or not. If the wearing resistance is serious, please maintain the ring die and countersink the wearing taped hole. The wearing compression rollers much be replaced. The wearing of the ring die holes affected the output greatly.
3. To adjust the clearance of the die and compression rollers. Too small clearance can increase the friction force of the compression rollers and ring die with short life span of ring die. Big clearance gives rise to slipping of the compression rollers with lower output.
-----------------------------------------------------------------------------------------------------------------------------------------
Machine to make Wood Pellets
Machine to make wood pellets or biomass pellets usually refers to pellet mill or pellet machine or pellet press, even pellet plant at large.There are still so many people within related industrial sectors not making full use of biomass material. As we know, biomass waste includes...
Machine to make wood pellets or biomass pellets usually refers to pellet mill or pellet machine or pellet press, even pellet plant at large.There are still so many people within related industrial sectors not making full use of biomass material. As we know, biomass waste includes...
News
- Small Pellet Machine Manufacturer-Kingman
- Application of Wood Pellets and Use of Biomass Pellets
- From Fossil Fuel into Biomass Pellet Fuel
- Biomass Pellet Making Machines Market
- Applying of pellet stoves for home use
- Highland pellets to build $130 million facility in arkansas
- How to deal with the blocked hammer mill
- How to Make Wood Pellets with Sawdust
- The government policy promotes the development of biomass fuel
- Market analysis of biomass pellet fuel
- Strategic positioning of renewable energy
- Biomass energy has pass through the pre assessment
- The key point of deep processing of biomass pellet
- Harbin is promoting the development of biomass machinery
- The development of biomass formation technology I
- The development of biomass formation technology II
- Biomass energy industry is now going full tilt in 2015
- Rapid increasing demand of sawdust pellet on the market
- Pellet fuel market in EU
- Chinese Biomass Energy Conference held in Beijing
- Future market development of straw pellet mill
- Peanut Shell Pellet Mill Makes High Quality Pellets
- The utilization of straw is only 5%, biomass energy needs our attention!
- Corn straw pellet machine relieves the tight supply of fuel energy
- Reasons for loose or not forming of biomass pellet mill