Sieve
Main use and scope of application
The rotary vibratory sieve (also referred to as sifter. sizing screen or classifying screen), on the one hand, is used to screen and classify powdery and granule materials for Pellet Plants or animal feed factories. On the other, the sieve can also be used to preliminarily sift materials or classify the semi-finished materials which have been second pulverized in large-medium size animal feed factories. Plus, it is too used in such sectors as grain and food production, chemical industry, sugar refinement, mining and paper making.
1. The features
Thanks to the lopsided balance design, the sieve features small vibration and low noise.
Due to the adoption of non-geared drive, there is no need of lubrication and oil leak can be avoided.
The sliding support to the end is replaced with elastic support frame so that its high efficiency in classification and low noise can be achieved.
The streamline design within the discharge outlet can keep materials from being precipitated and the odds of cross contamination can further be reduced.
The pressure sieve design facilitates sieve changes.
2. Working principles
The driving force will be transmitted to gearings by motor via V-belt so that the sloped sieves will finally be driven. Due to the eccentric gear on the actuating device, from the feeding to the discharge part, the sieve trajectory will change from the circular to the elliptic and then to the approximately reciprocating linear way. Based on the circular motion of the sieves, all the material will not only be dispersed on the sieve surface rapidly and uniformly, but be classified automatically as well. All the smaller material will be easily sifted out while the bigger will move forward to the discharge hole along with the sieve slope. During the above process, smaller material will move against the sieve surface and be easily sifted out. To the discharge end, in light of the approximately reciprocating linear motion of the sieve becoming weakening, pellets bigger than the sieve meshes will flow to the discharge hole rapidly, effectively preventing material from clogging meshes so that the sifting high efficiency can be assured. The balancing part within the actuating device can balance inertia forces from all directions so that the sieve motion will remain steady.
The sizing screen is made up of two or three layers of sifter meshes, namely, the pellets can be re-sifted on the lower layer from being previously sifted on the upper. The pellets thus can be divided into three or four different categories as big, medium and small sizes.
Technical parameters:
Model |
Sieve Size(mm) L*W |
Layers |
Sieve Specs. Upper/Medium/Lower |
|||
SFJH110*2C | 2000 | 1097 | 2 |
Z5 10*10*d1.4 |
Z20 10*10*d0.55 |
14*14 |
SFJH130*2C | 2180 | 1297 | 2 |
Z5 10*10*d1.4 |
Z20 10*10*d0.55 |
14*14 |
SFJH130*3C |
2180(upper) 2000(lower) |
1297 | 3 | 10*10*d1.4 | 10*10*d0.55 | 14*14 |
SFJH150*2C | 2790 | 1497 | 2 |
Z5 10*10*d1.4 |
Z20 10*10*d0.55 |
14*14 |
SFJH150*3C |
2790(upper) 2600(lower) |
1497 | 3 |
Z5 10*10*d1.4 |
Z20 10*10*d0.55 |
14*14 |
Supplementary:
From time to time, Raw material needs sifting as much as pellet does. In this regard, another model of sieve can be offered by Kingman as well to handle purification of material yet with low costs in pellet plants or other industries.
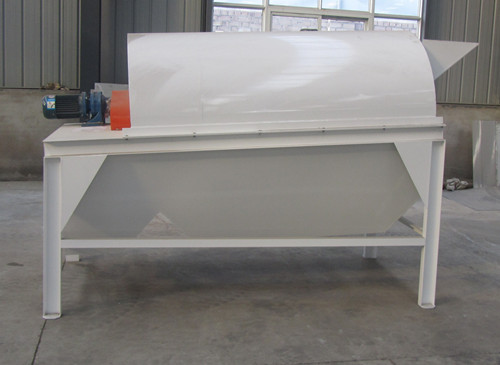